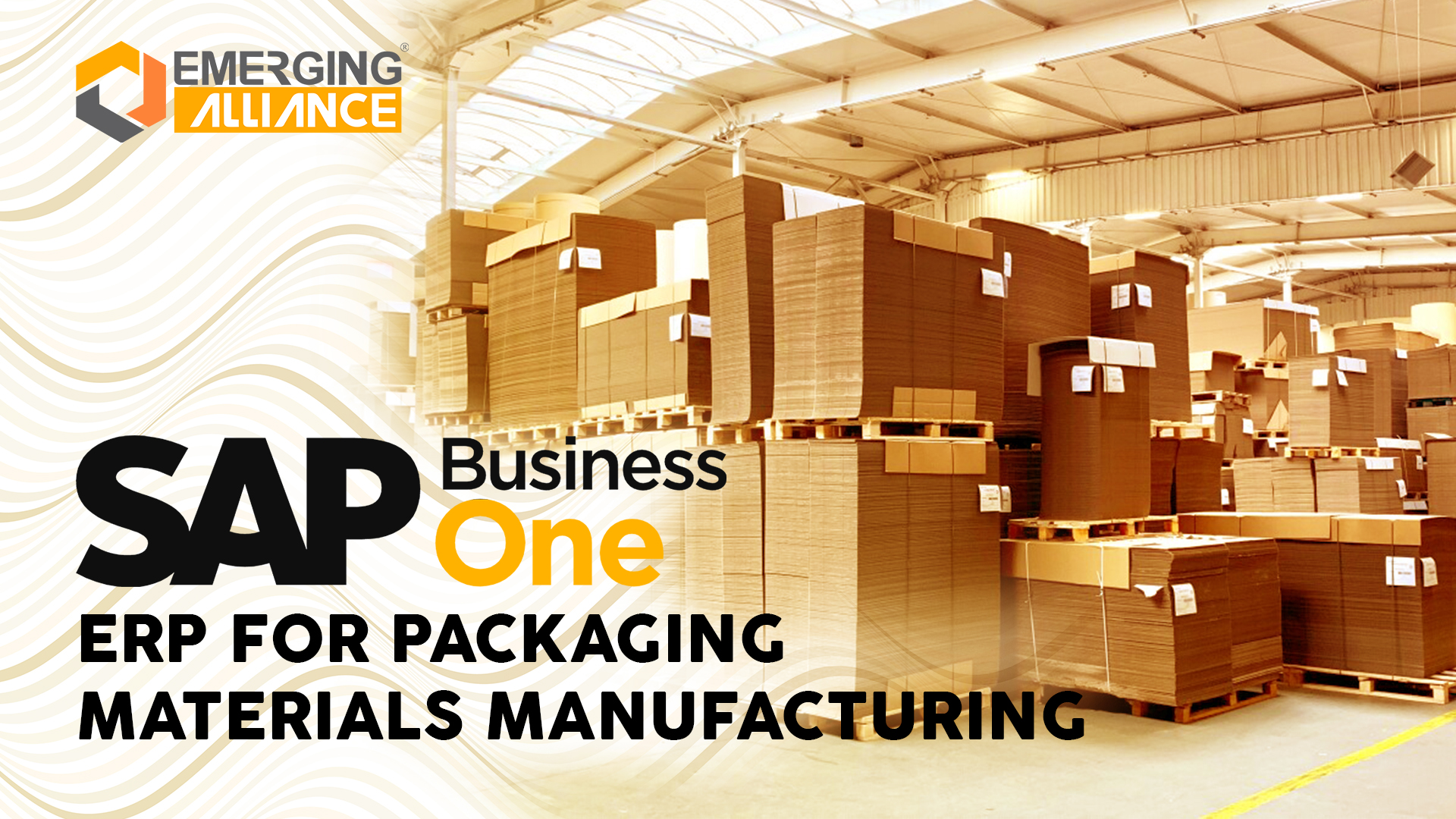
SAP Business One ERP FOR PACKAGING MATERIALS MANUFACTURING
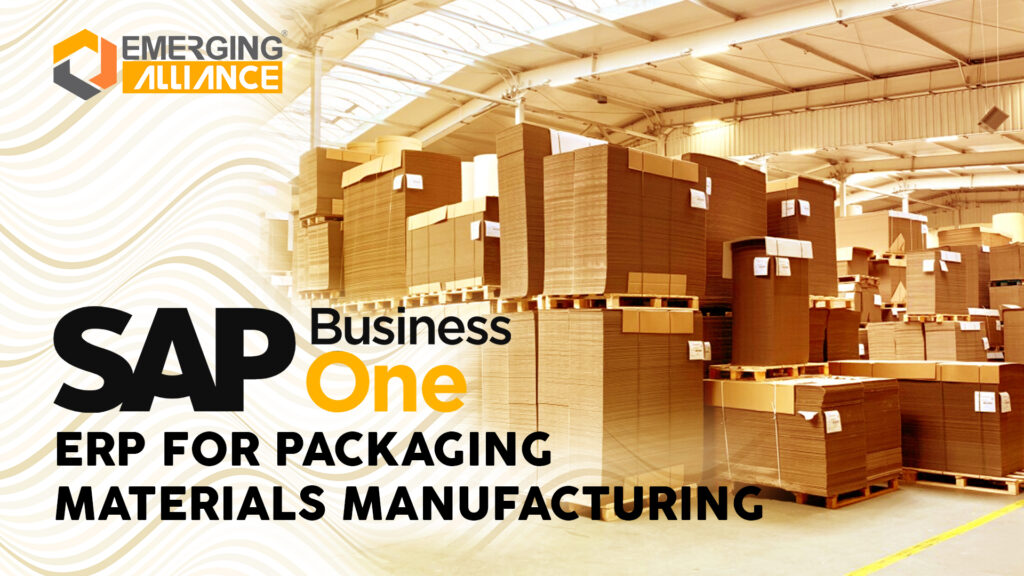
SAP BUSINESS ONE PACKAGING AND INVENTORY MANAGEMENT | ERP for PACKAGING
Vertical :
Packaging Products Manufacturer
Order to cash:
Full flow from Order Management (On basis of Sales Order – Production is planned)- Credit Management – Order fulfillment – Order Shiping – AR Customer Invoicing – I/P – Reports run in a controlled way from SAP B1 ERP Software.
Procure to pay:
Integrating purchasing and accounts payable systems in SAP B1 to create greater efficiencies with reports. We run an MRP wizard which auto creates PR on the basis of BOM(Job Work) {Min Order quantity is a critical factor for procuerment} – which is converted to Purchase order against which Goods receipt is done by stores as per its Accounts makes Payable invoice and Outgoing payment.
Sales order:
SO is created once PO is raised or Quotation is confirmed by the Customer in SAP Business One. Using DMS PO softcopy is also attached. Payment terms and Delivery date is auto fetched as per the customer master. (Committed limit management help to control){If the customer asks for an estimated quote BOM is also revised and the order is created}
Sales Quote:
To submit a quotation first we have to estimate the cost by evaluating RM used with properties such as (GSM, Flute, Reel, Bursting factor, etc) and factors such as (No of Ply, No of Outs, Linear Matrix, Length, No of Boards, Sheet Area, etc) and as per requirement formula will be set and the price will be auto-calculated. Way SAP Estimation Sheet helps us to get the Sales Cost Estimated as per it – Sales quotation is created from SAP. The Ship to and Bill to fields are automatically populated with data entered in the Business
MRP :
Used for Plan to produce by which auto Production order and auto Purchase request is also created (Material Requirements Planning (MRP) enables you to plan material requirements for a manufacturing or procurement process)
Purchase Request :
PR is auto-created by Material Requirements Planning and even PR is created manually department-wise as per their requirement of office equipment, consumables, etc against which PO is generated.
Purchase Order:
PO is created by approval procedure and pdf is mailed to the vendor directly from SAP. Critical aspects for procurement such as GMS, length, quality, min order qty, in stock, qty in order, preferred vendor, etc data is visible in a single screen view for proper analysis by which our procurement process is accurate and changes of error reduced to a great extent.
GRPO :
On basis of PO when Vendor delivers item, Goods receipt against PO is posted which debits the inventory(Inventory management and Inventory reports standard IN SAP B1)
Supplier Payment:
On basis of GRPO, AP invoice is added against which Outgoing payment is done
Production:
As per BOM , considering demand and stock weekly MRP is run – Production orders are auto-created. Further once PRD ORD is released, Route stages wise (Corrugation, Printing (single side), UV, Lamination, fluting, pasting, die cutting, trimming, stripping, gluing, packing) RM are issued and receive the FG produced item into inventory and report completion for the production order is done. (Product Costing, variance report, resource capacity planning is critical aspects of SAP.)
Invoice:
Account Payable / Receivable invoice creation and as per it payment entries is posted. (Open document system give a proper control)
Service:
Facility management is done using a service module.
Visit Us: https://www.emerging-alliance.com/