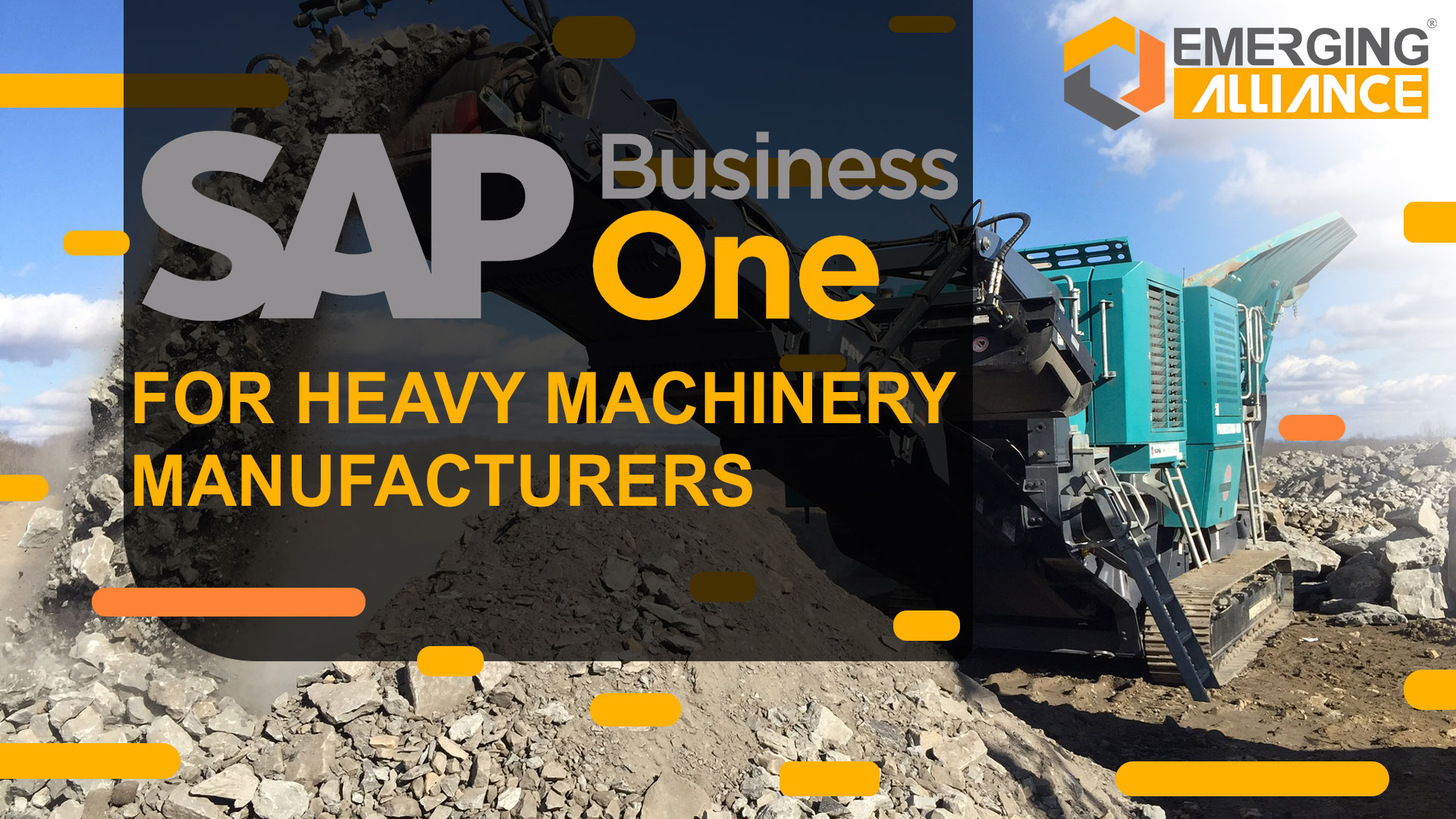
SAP Business One / SAP B1 ERP for Heavy Engineering Industry
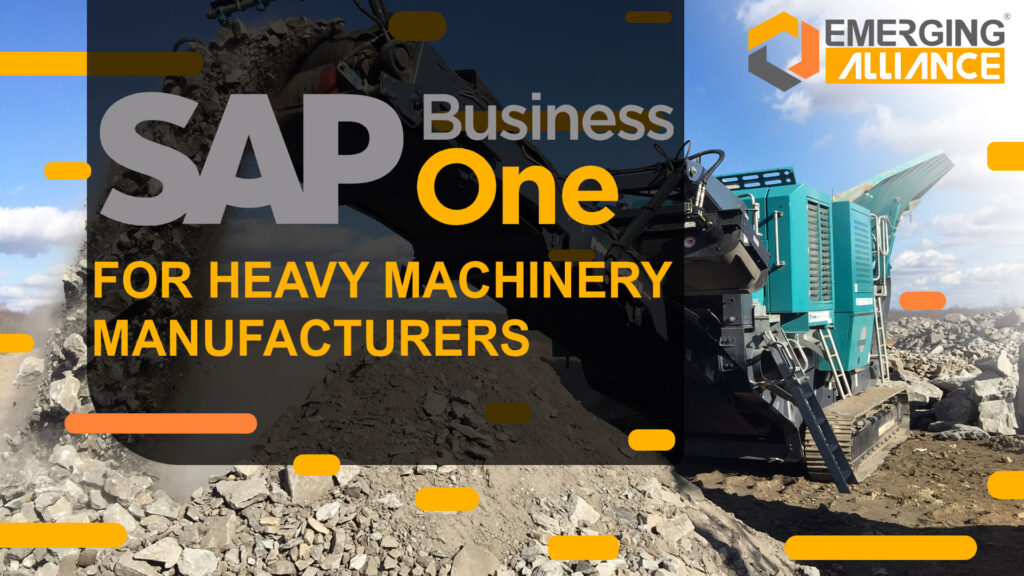
SAP B1 for Heavy Machinery Production and Service
Worldwide, the heavy machinery industry is experiencing exponential growth, placing immense pressure on service providers in the machinery and components sector. The scale of work, which includes project management, loading of heavy machinery, transportation, warehousing, and other tasks, presents significant challenges. Transportation issues and the need for seamless integration across different departments further compound these challenges. SAP Business One, a world-class ERP system tailored for the machinery manufacturing industry, addresses these concerns by integrating processes and enhancing efficiency and productivity.
To adhere to safety standards, such as ensuring mechanical components withstand strain and pressure vessels, companies must produce quality products meeting customer needs. SAP Business One, a flexible manufacturing management system, assists companies in reducing production and supply chain management costs while complying with safety regulations.
Efficiency and accuracy are crucial for heavy machinery manufacturers producing items like jaw crushers, impactors, conveyors, and feeders. Managing production for various clients and products in the same facility without errors is a daunting task. Additionally, clients increasingly demand quick design changes, last-minute orders, and shorter lead times. Amidst fierce competition, thin margins, and stringent quality compliance, SAP Business One for Heavy Engineering Industry proves invaluable in streamlining complex manufacturing processes, resulting in increased efficiency, reduced lead times, and higher revenues.
An essential feature for ERP systems in the machinery manufacturing industry is integration with CAD software. Manufacturers rely on CAD drawings to generate Bills of Materials (BOMs), which serve as inputs for tasks like raw material ordering, generating job cards, and billing. SAP Business One for Heavy Engineering Industries seamlessly integrates with CAD software, automating BOM generation from CAD designs. This integration facilitates handling custom jobs, where design changes are common. SAP Business One swiftly identifies design modifications, updates the BOM, and transmits the changes to other functions, ensuring accuracy and efficiency.
Benefits for the machinery and components industry with SAP Business One include:
- Rapid growth facilitated by a flexible, innovative solution.
- Optimized production processes.
- A comprehensive view of the company with analytics for continuous improvement.
- Streamlined business processes adaptable to market needs.
- Enhanced integration for effective time and resource utilization.
Let’s delve into the order processing cycle in the machinery industry with SAP Business One:
Order to Cash Cycle with SAP Business One for Heavy Engineering:
Upon receiving a customer purchase order, a sales order is created in SAP Business One. Once the finished goods (FG) are manufactured, an accounts receivable invoice is generated. Reports such as customer receivables, cash flow, and sales analysis are crucial for monitoring incoming payments.
Planning with SAP Business One for Heavy Engineering:
Based on received sales orders, the MRP wizard is run monthly in SAP Business One, considering BOM and stock levels. Purchase requests for buy items and production orders for make items are automatically created. Reports like order recommendations aid in planning.
Procure to Pay with SAP Business One for Heavy Engineering:
Following purchase requests generated by MRP, the purchase team creates purchase orders. Upon goods receipt by the stores team, stock is accounted for in inventory. Accounts payable invoices are processed, and outgoing payments are made accordingly. Major reports such as purchase payables, cash flow, and purchase analysis are vital for managing procure-to-pay processes.
Production:
Raw materials are issued stage-wise as per the work order created from MRP. Upon completion of production, FG is received into stock. Costing and variance reports play a significant role in monitoring production costs.
Service:
Each FG item is assigned a serial number, enabling the creation of equipment cards for servicing purposes. Any expenses incurred during service, including part replacements, are recorded accordingly.
In conclusion, heavy metal manufacturers encounter various challenges, including business complexities, high-value clients, thin margins, and increasing globalization. However, these challenges can be mitigated by deploying advanced ERP systems like SAP Business One, which streamline operations and ensure relevance to clients both now and in the future.
If you would like to know more about our ERP services, please visit us at: https://www.emerging-alliance.com/
Join the ranks of the inquisitive – Delve into captivating content on our website and uncover more than you ever imagined!
Want to speak to an expert? Fill in the form below, and we will be in touch with you shortly!