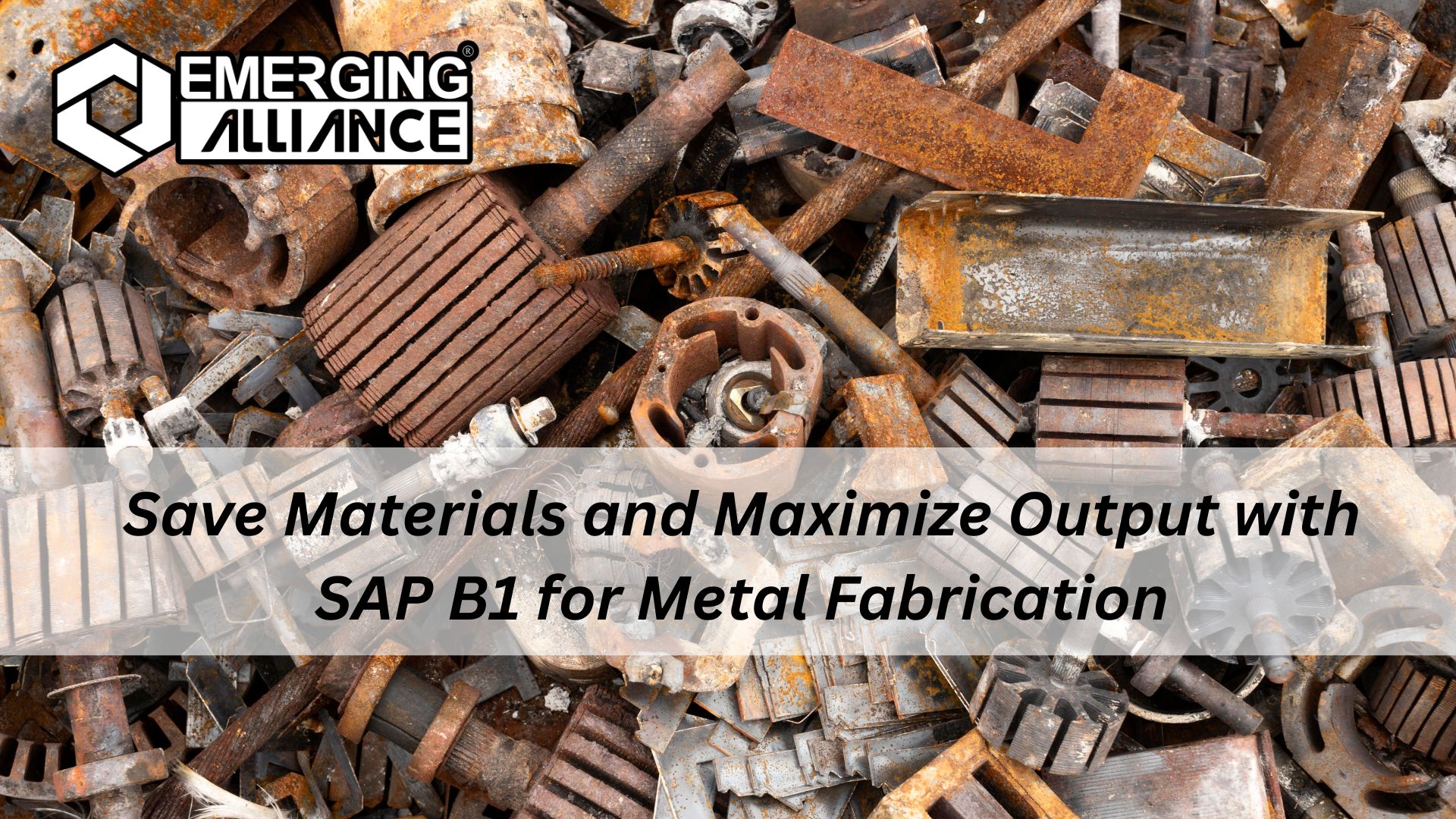
Save Materials and Maximize Output with SAP B1 for Metal Fabrication
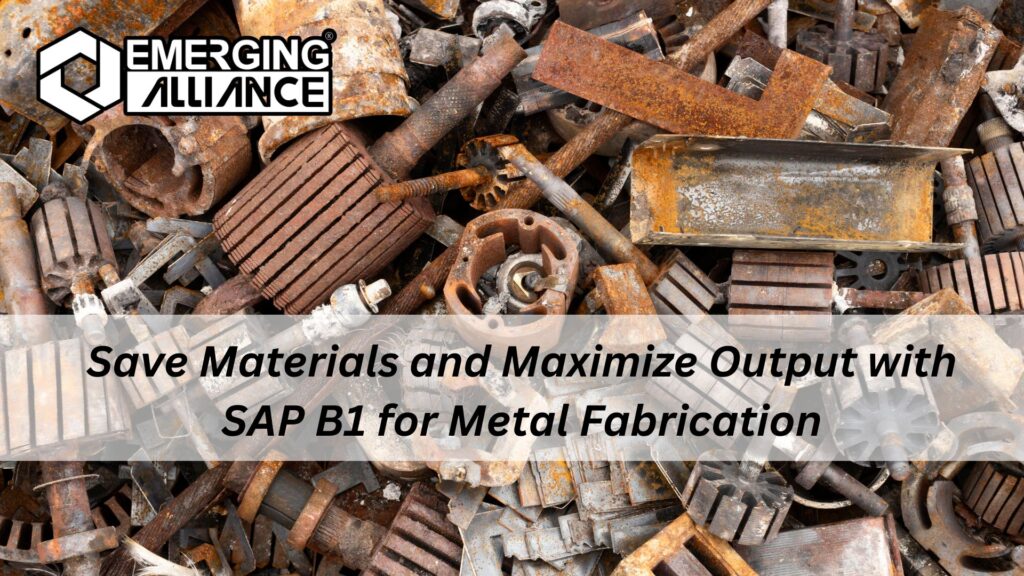
Maximize Output and Minimize Material Waste with SAP B1
Material wastage and scrap can quietly eat into profits in the metal fabrication industry. Whether it’s due to inaccurate planning, leftover off-cuts, or rework, unmanaged scrap leads to increased costs and lower margins. Enter SAP Business One (SAP B1) — a powerful ERP solution built for small and mid-sized manufacturers. SAP B1 helps metal fabricators gain control over materials, optimize output, and improve profitability with real-time data and automation.
⚙️ The Real Cost of Scrap in Metal Fabrication
Material waste in fabrication doesn’t just mean discarded metal. It includes:
- Incorrect cutting due to outdated drawings
- Poor nesting or layout planning
- Lack of scrap tracking and recovery
- Rework caused by missing quality checkpoints
- Over-ordering due to inaccurate stock data
Each of these issues reduces efficiency, lowers margins, and hurts delivery performance.
🚀 How SAP B1 Helps Save Materials and Boost Output
✅ 1. Precise Inventory and Raw Material Tracking
Track exact quantities of steel, aluminum, copper, or any other material used per job. Avoid overuse, stockouts, and unplanned purchases with real-time inventory data.
✅ 2. Smart Job Routing and Nesting Integration
Integrate SAP B1 with CAD/CAM tools or nesting software to minimize sheet waste and improve cut planning. Reduce leftover scrap and maximize raw material yield.
✅ 3. Live Production Monitoring
See the real-time status of jobs, machine usage, and material flow. This allows you to:
- Stop overconsumption early
- React to production issues quickly
- Improve machine efficiency through smarter scheduling
✅ 4. Scrap Management and Reuse
- Identify recurring waste sources
- Reuse leftover materials in other jobs
- Improve vendor selection and machine settings
- Identify recurring waste sources
- Reuse leftover materials in other jobs
- Improve vendor selection and machine settings
✅ 5. Job Costing and Waste Analysis
Measure actual vs. planned material usage. Track material costs per job or per shift. Use insights to improve future quoting and reduce margin loss due to wastage.
✅ 6. Quality Checks that Prevent Rework
Set up inspection checkpoints to catch errors early. SAP B1 ensures that only compliant parts move to the next stage — reducing scrap from rework or rejects.
📊 Business Benefits You Can Expect with SAP B1
- 📉 Up to 20% reduction in raw material wastage
- ⚙️ Higher machine efficiency through better planning
- 📈 Increased output per shift
- 💰 Improved job profitability and quote accuracy
- 📋 Full traceability from material receipt to finished product
Conclusion
In a competitive market, saving materials isn’t just about cutting costs — it’s about building a smarter, leaner, and more profitable fabrication operation. With SAP Business One, metal fabricators gain the visibility, control, and insights they need to reduce waste, maximize output, and scale with confidence.
Also read, similar articles that interests you on SAP Business One for Metal fabrication industry.
FAQs
1. How does SAP B1 help reduce material waste in metal fabrication?
SAP B1 tracks material usage per job, monitors inventory in real time and helps identify scrap and rework patterns to reduce waste.
2. Can SAP B1 track leftover materials and scrap?
Yes, it allows you to record, categorize, and reuse scrap materials—helping reduce overall material loss.
3. How does SAP B1 improve production output?
By optimizing job scheduling, reducing downtime, and improving material planning, SAP B1 helps maximize daily production output.
4. Can I integrate SAP B1 with nesting or CAD software?
Yes, SAP B1 can integrate with third-party CAD/CAM and nesting tools for better cut planning and raw material optimization.
5. Does SAP B1 support real-time production monitoring?
Yes. You can track job status, machine usage, and material flow in real time for faster decision-making and error correction.
6. How accurate is the job costing in SAP B1?
SAP B1 provides real-time job costing by tracking actual vs. planned material, labor, and overhead — helping improve profit margins.
7. What kind of reports can SAP B1 generate to analyze waste?
You can generate reports on scrap trends, material usage efficiency, variance analysis, and cost per job for better decision-making.
8. Will SAP B1 help us prevent over-ordering raw materials?
Yes. With accurate inventory levels and MRP (Material Requirements Planning), SAP B1 helps avoid overstocking and underutilization.
9. Can SAP B1 help reduce rework due to quality issues?
Absolutely. You can set up inspection checkpoints to catch defects early and prevent defective parts from reaching the next stage.
10. Is SAP B1 suitable for small and mid-sized metal fabrication companies?
Yes, it’s specifically designed for SMEs and is scalable as your operations grow.
💡 Ready to transform your Metal Fabrication Operations with SAP B1? Contact us today!